Research areas
Research within the RS2E revolves around two pillars: The main research areas and the transvere axes which bring together all the necessary expertise to carry out the projects initiated within the research themes.
RESEARCH AREAS
- Advanced M-ion: Dedicated to the Metal-ion (Li,K,Mg,Na) technologies, it will address the locks at the electrode materials, electrolytes and formulation in order to increase their performances, reliabilities and safeties.
- Capacitive storage: Supercapacitors form the backbone of this theme. The researchers are looking to improve the production of microporous carbon electrodes and the formulation of new electrolytes such as ionic liquids.
- Eco-conception and recycling: It will be dealing with problems of recycling and lifecycle analysis of materials and storage systems. It will also favor new concepts of renewable electrodes and the development of innovative syntheses based on bio-inspired, biomimetic and/or bio-assisted approaches.
- Sensing and self-healing: With battery cells becoming the heart of future society, there is a crucial need to increase their quality, reliability and life time by non-invasive operando performance monitoring and the possibility to repair defective components.
- Interfaces : This thematic focuses on the understanding and the control of the “natives” and “artificial” interfaces in the batteries to improve their performances and their lifetime.
TRANSVERSAL AXES
- Theorie : In interaction with the experimentalists, the «Theory» group develops methods and strategies in order to guide the search for new materials, simulate the experiment and predict the electrochemical and chemical stability of the electrodes and electrolytes.
- Analytical platforms
- Pre-transfet unit
- Safety : Its activities are mainly focused on the implementation of advanced electrochemical tests/protocols and post-mortem studies of batteries and supercapacitors to determine the causes of their malfunction and provide optimized solutions.
OUR ACHIEVEMENTS
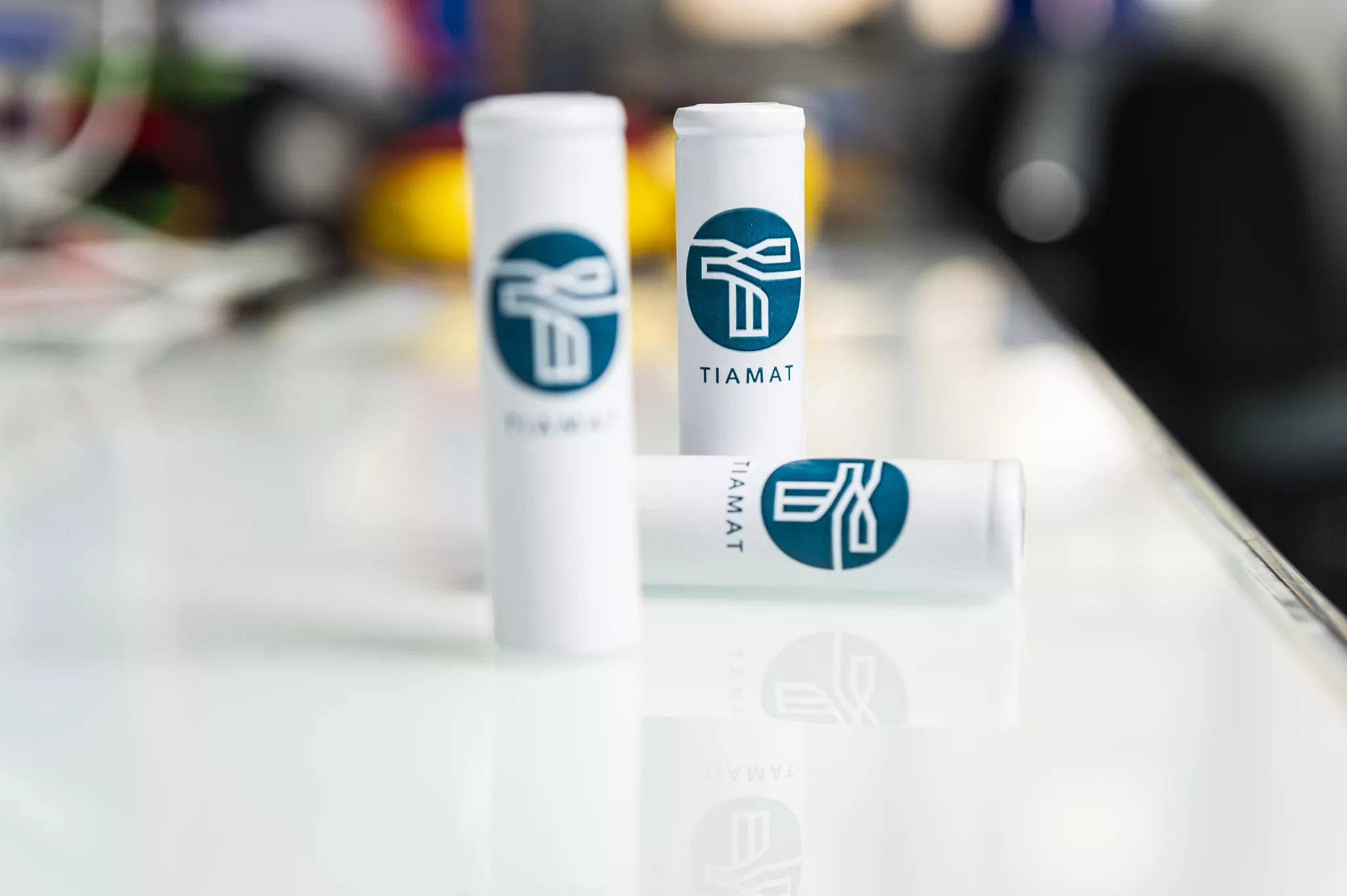
Tiamat - Develops, produces and markets Na-ion batteries